Flux cored arc welding (FCAW) offers advantages over solid wire processes, which is why it’s so popular. As a result, it’s used in structural steel erection, heavy equipment repair, bridge construction and other applications. FCAW offers high deposition rates, excellent chemical & mechanical properties, and additional weldability required for these jobs.
Common FCAW Problems 9-23.pdf
Download
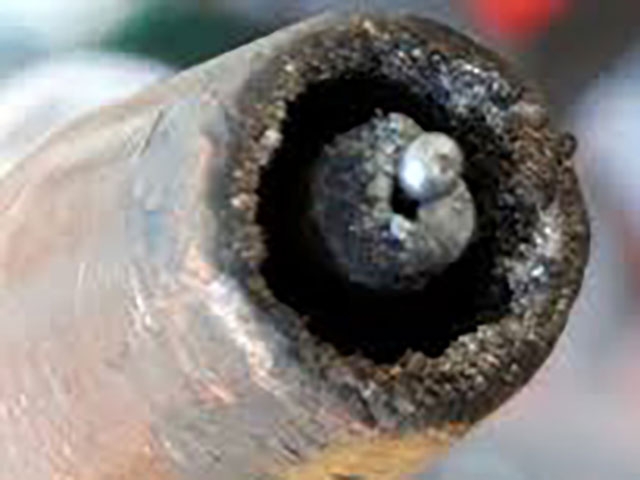
The two most prevalent wire feeding problems are burnback and birdnesting. These result in a prematurely extinguished arc, which may cause weld quality or appearance issues.
How to avoid them:
Burnback is when the wire melts into a ball at the end of the contact tip and often results from slow wire feed speed, holding the gun too close to the workplace, or dirty, clogged, damaged liners and contact tips. Prevent this from happening by using the correct feed speed for your application, maintain an optimal distance from contact tip to the workpiece of no further than 1 ¼” and by cleaning the drive rolls and blowing out the liner weekly. Also, keep things in good working condition and replace components as necessary to reduce downtime and frustration.
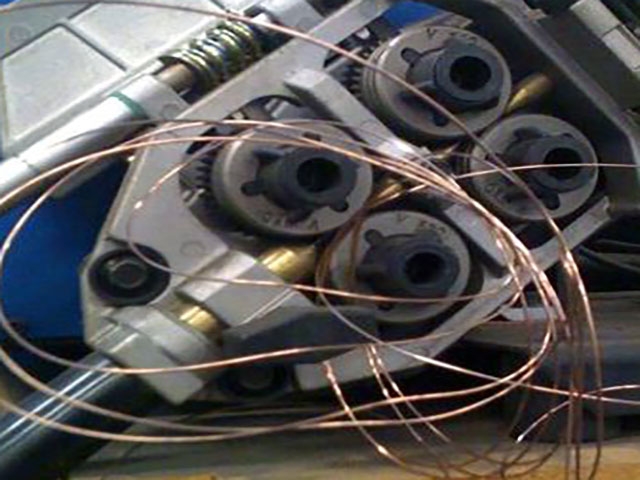
Birdnesting, on the other hand, happens when wire gets tangled, stopping the feeding process. To prevent it, use a knurled V-groove or U-groove drive roll in your wire feeder. Then, make sure to set them at the correct tension which is usually on the lower pressure end as FCAW is tubular and therefore more prone to crushing.
Other causes of birdnesting? A liner blockage, improperly trimmed liners, or the wrong liner. If your liner is blocked or damaged, replace it. Follow manufacturer recommendations for trimming, and make sure it doesn’t have burrs or sharp edges. Finally, use the correct size for liner for your diameter of welding wire.
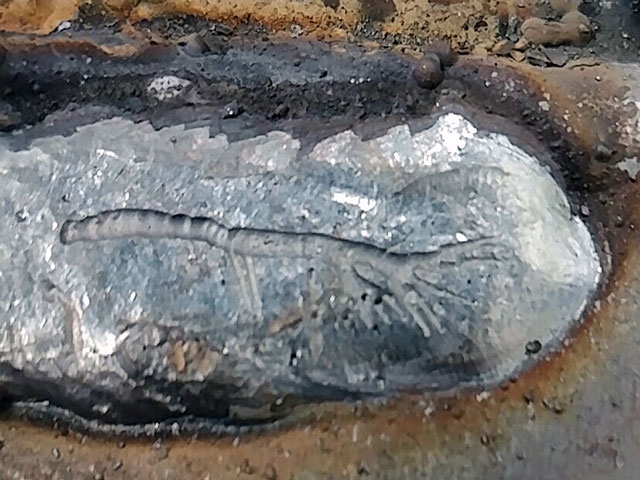
Porosity happens when gas becomes trapped in the weld metal. Worm tracking, on the other hand, are longitudinal voids on the surface of the weld bead caused by gas trapped beneath the solidified slag layer and molten weld metal underneath. Both discontinuities may or may not have to be repaired based on the welding code you are working to.
How to avoid them:
To prevent porosity, remove rust, grease, paint, coatings, oil, moisture and dirt from the base metal. Use filler metals with added deoxidizers to better weld through contaminants, but don’t replace cleaning with these. Also, contact-tip-to-work-distance (CTTWD) should be kept between 3/4 to 1-1/4 inches. If you are using a gas-shielded type flux core, make sure you have adequate weld joint protection from wind or air currents and proper gas flow between 30-45 CFH
To stop worm tracking, excessive voltage is often the culprit. Follow the parameters recommended by the executive data sheet. If worm tracking happens, cut the voltage down little by little, in one-half increments. Other common causes are weld joint contamination, filler metal that has been exposed to the atmosphere for too long and has absorbed moisture, or excessive weld bead size in a single-pass weld.
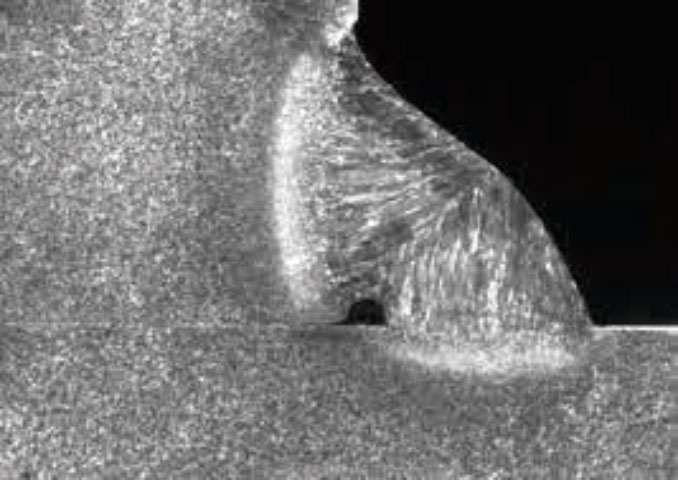
Inclusions happen when the slag generated by the molten flux gets trapped inside the weld. Generally, they can be prevented by adjusting welding techniques.
How to avoid them:
There are four main causes of slag inclusions, all related to welding techniques:
Incorrect bead placement
Be certain to provide sufficient space in the weld joint for additional passes, particularly on joints requiring multiple passes.
Using a pushing technique instead of dragging
For slag producing electrodes you should always push when welding as opposed to dragging to prevent slag inclusions
Not maintaining the correct travel angle and travel speed
In flat, horizontal and overhead positions your drag angle should be between 15 and 45 degrees. In vertical up position, your angle
should be limited to between 5 and 15 degrees. Travel speed should be steady and not to slow to prevent the weld puddle from flashing ahead of the arc and creating inclusions.
Not cleaned thoroughly between weld passes
Be certain to clean thoroughly between weld passes, removing any slag with a chipping hammer, wire brush or grinding before beginning your next weld pass. Certain executive cored wires have self peeling slag which also help eliminate the issue of slag inclusions.
Flux cored arc welding is a dependable process across various industries and applications. Achieving top-tier welds through FCAW isn't left to chance; rather, it hinges on proficient welding techniques, precise parameter selection, and your capacity to pre-empt issues or promptly address them when they arise.
Bear in mind that equipping yourself with this fundamental knowledge empowers you to proactively avoid the obstacles that can come along with FCAW welding, all while preserving both time and the quality of your work.
- Home
- News
- Contact us
- Stainless Steel
- Carbon Steel
- Nickel Alloy
- Low Alloy
- Aluminum
- Cobalt-Hardfacing
- Executive Line Card
- Find a Distributor
- Become a Distributor
©2024 Executive Filler Metals. All Rights Reserved.