Shielding gases primarily safeguard the molten weld pool from atmospheric contaminants such as oxygen and nitrogen. They also influence the mode of weld transfer, the depth of weld bead penetration, the stability of the arc, the mechanical characteristics, and the overall quality of the completed weld.
Shielding Gases and Welding 4-24.pdf
Download
The GTAW process can weld all types of metals, primarily using Argon as the shielding gas. Argon, an inert gas, does not react with metals, ensuring that the non-consumable tungsten electrode, which generates the welding arc, remains uncontaminated. This makes Argon suitable for welding both ferritic metals like steel and nonferrous metals such as aluminum. For welding thicker aluminum, a mixture of Argon and Helium—an inert gas that provides greater heat and penetration—may be employed. Additionally, Argon-Hydrogen mixtures are utilized in welding austenitic stainless steels, as well as nickel-copper and nickel-based alloys.
The GMAW process is utilized to weld a wide variety of metals, including both ferrous and nonferrous types. The four most used gases in GMAW are Argon, Helium, Carbon Dioxide (CO2), and Oxygen (O2). Argon and Helium are inert gases that can be used individually or in combination. However, using Argon alone is generally not recommended for welding steel and other ferrous metals due to its insufficient thermal conductivity, which fails to produce a fluid weld pool. This deficiency often leaves the outer edges of the arc cold, resulting in a high, peaked weld bead shape with undercutting and a narrow penetration profile. Such outcomes might not meet certain welding standards.
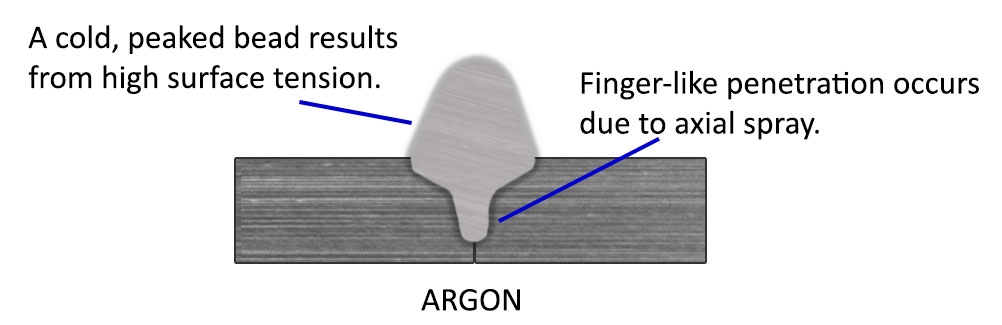
Carbon Dioxide (CO2) is a reactive gas and is unique in that it can be used in its pure form for welding ferrous metals like steel. CO2 as a shielding gas enables deeper and wider weld penetration, particularly on thicker plates. However, this comes with drawbacks: the arc stability is reduced and there is an increase in spatter compared to when CO2 is mixed with an inert gas like Argon. These effects are demonstrated in below.
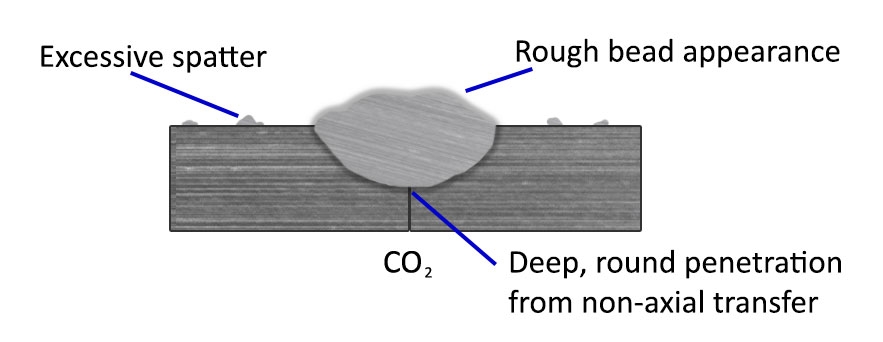
Today, most shielding gases for GMAW (Gas Metal Arc Welding) of steel consist of a mixture of Argon and CO2. For welding thin steel ranging from gauge thickness to 3mm, a common mixture used is 25% CO2 and 75% Argon, which facilitates short circuit transfer. This method of arc transfer allows welding in all positions and is particularly effective for lower current ranges with smaller electrode diameters. It produces a small, quickly solidifying weld pool that is ideal for thin materials and offers good control during out-of-position welding and over larger root gaps.
Reducing the CO2 content to between 8% and 15% in an Argon mixture allows for an increase in current and achieves spray transfer, which is suitable for welding materials thicker than 3mm. Spray transfer, occurring at higher current ranges, creates a larger weld pool primarily used for flat and horizontal welds. The adoption of pulsed GMAW transfer, which alternates between high peak currents and lower background currents hundreds to thousands of times per second, facilitates spray transfer while enabling welding in all positions.
For enhanced weld metal fluidity, Oxygen-Argon mixtures are also used. A mixture like 2% Oxygen in Argon can achieve spray transfer and is applicable for welding both steel and stainless steel. Figure 3 illustrates the varying weld penetrations and profiles obtained with these gas mixtures.
When it comes to welding nonferrous metals like Aluminum, the most prevalent shielding gases are either 100% Argon or a mixture of Argon and Helium. These gases ensure optimal weld quality and characteristics for nonferrous applications.
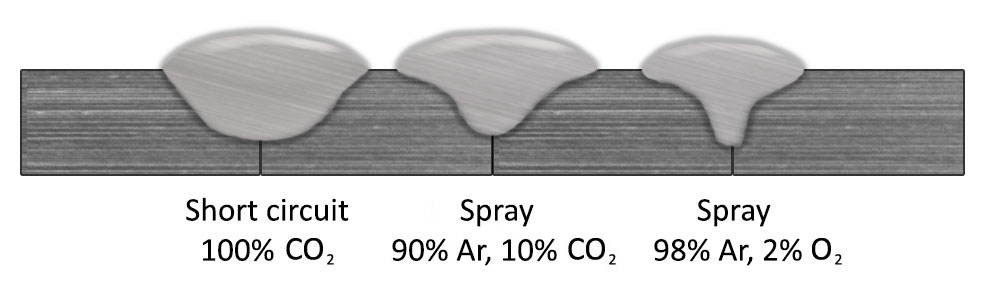
Flux Cored Arc Welding (FCAW)
The FCAW process commonly employs 100% CO2 as a shielding gas for welding steel or austenitic stainless-steel alloys. FCAW filler wires are specifically formulated to be compatible with 100% CO2, and with the appropriate selection of consumables, they can be used for welding in all positions. The arc transfer type when using 100% CO2 is globular, which provides deep weld bead penetration. However, for a smoother and more stable arc, the use of Argon-CO2 shielding gas mixtures is often recommended. The most prevalent mixture for this purpose is 75% Argon and 25% CO2, which balances arc stability with effective penetration and weld quality.
Metal Cored Arc Welding (MCAW)
The MCAW process typically employs Argon-CO2 gas mixtures for shielding. It is specifically designed to operate in the spray transfer mode, utilizing a mixture of 8% to 15% CO2 in Argon to achieve optimal spray transfer conditions. This configuration is particularly effective for welding in flat and horizontal positions, where the characteristics of spray transfer—such as a smooth, stable arc and deep, uniform penetration—are most beneficial. This mixture helps ensure high-quality welds with reduced spatter and excellent surface finish.
The welding processes and gas mixtures mentioned are among the most used in today's fabrication industry. However, there are numerous other options available that can be tailored to specific applications. For these specialized needs, consulting your executive distributor is advisable.
- Home
- News
- Contact us
- Stainless Steel
- Carbon Steel
- Nickel Alloy
- Low Alloy
- Aluminum
- Cobalt-Hardfacing
- Executive Line Card
- Find a Distributor
- Become a Distributor
©2024 Executive Filler Metals. All Rights Reserved.