Filler metals such as stick electrodes and cored wires that become damaged, either by moisture or contaminants, cause poor weld quality. It is important to follow best practices with regards to storage and handling.
Storage and Handling 2-24.pdf
Download
Executive filler metals come in packaging designed to shield them when kept indoors under clean and dry conditions, where temperatures remain above 4°C (40°F) and the relative humidity does not exceed 60%.
Maintaining a consistent temperature is vital to prevent condensation on the consumables.
Ensure consumables are stored in locations safe from rain and snow, elevated from the ground, distanced from walls, and in their intact, original packaging, whether on delivery pallets or storage racks.
Avoid stacking pallets more than two layers high to eliminate risks of tipping and potential harm to the packaging and the welding consumables.
For storing consumables that are in use, remove the spool from the wire feeder, encase it in a clean plastic bag with a desiccant, and seal it well. Then, place it back in the original box and store it in a dry area.
If these measures are not possible, firmly cover the welding wire spool with a plastic bag on the feeder. Additionally, always reattach the lid on wire drums when they are not in use.
When used outdoors or in unheated spaces, remove wire from the feeder after use and place it in a heated storage area if not used within 8 hours. Opened packages can be stored for up to 24 months, provided there's no rust or color changes on the wire. Discard any wire exposed to moisture or showing signs of rust.
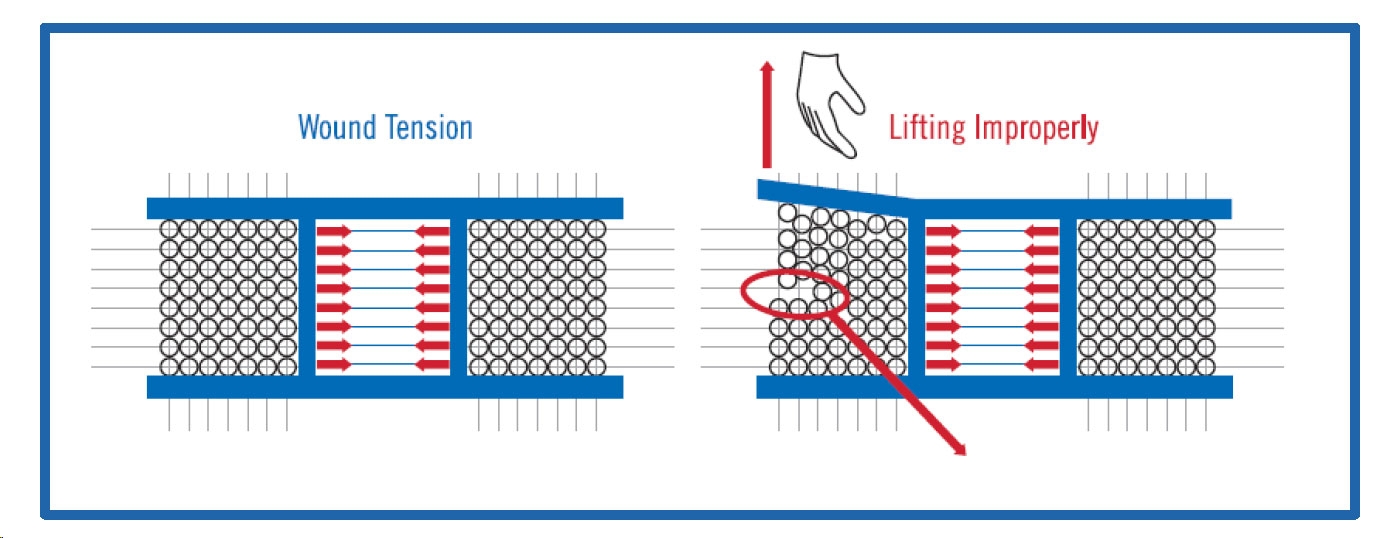
It's essential to wear gloves when handling consumables to avoid transferring moisture from your hands, which could lead to rust, especially on solid wires. Rust formation can lead to porosity issues or problematic wire feeding. Once solid welding wire has been compromised by moisture, it cannot be restored.
To ensure optimal welding performance and maintain weld quality, it's crucial to store your welding wires in a place that is free from water, grease, oil, and other debris. These substances can negatively impact your welding process, affecting both productivity and costs. Operations like oxy-fuel cutting or carbon arc gouging should be performed at a distance from welding wires and welding areas. The dust from these activities can settle on the wires, leading to feeding difficulties or blockages in your contact tip and nozzle, which can cause an unstable arc.
If welding must be performed in conditions prone to moisture, rain, snow, sea spray, or dust, consider using a wire feeding system with a protective casing.
When carrying a spool, lift it vertically from the bottom, not by the flange, else spatial deformation can form gaps in the winding that can cause wire to slip in and subsequently get tangled.
In some cases, it may be possible to restore electrodes and cored wires to usable conditions by putting them through a reconditioning process.
Electrodes
Moisture poses the greatest threat to stick electrodes, as it can lead to issues such as porosity, hydrogen-induced cracking, and the subsequent downtime and expense incurred from rework to address these defects.
To recondition stick electrodes, remove the electrodes from their original packaging and place them in the re-baking oven, ensuring they are stacked to a maximum height of 2 inches to guarantee a thorough bake-out. Refer to the specific guidelines below for detailed instructions. The timing for reconditioning should begin once the electrodes reach the oven's set temperature.
For added precaution, it's suggested to re-bake electrodes prior to use, even if they have been stored under optimal conditions.
It is important to keep cans or cartons of stick electrodes, especially low-hydrogen types like Executive PLUS 7018-1, sealed when not in use, whether in a workshop or onsite. Stick electrodes should be kept in a rod oven that maintains them at ideal operating temperatures. Always reseal the packaging after removing the electrodes you need.
Post re-baking, coated electrodes ought to be kept in specially designed rod ovens at a controlled temperature between 120°C (250°F) - 176°C (350°F) and used within 3 weeks to maintain their integrity.
Cored Wires
To achieve optimal performance, it is advised to utilize Executive cored wires within a week of the package being opened. Should there be any cored wire left unused, it can be taken out of the plastic bag and kept in a dry rod oven. The temperature should be maintained at no more than 150°C (300°F) for wire spool baskets and 52°C (125°F) for plastic spools.
If low alloy and carbon steel flux cored wires show signs of weld metal porosity or "worm tracks," which are often the result of the core materials absorbing moisture, a re-baking process may restore them. Coils or wire baskets containing these products can be re-baked at 150°C (300°F) for a period of 6-8 hours.
Stainless flux cored wires on wire baskets, once removed from their plastic bags, can be subjected to re-baking at temperatures ranging from 150°C (300°F) to (176°C) 350°F for 6-8 hours.
Similarly, nickel flux cored wires, whether on wire baskets or fiber spools, can be taken out of their plastic bags and re-baked at a temperature between 104°C-121°C (220-250°F) for 8-10 hours.
If the wire still shows an erratic arc, porosity, or "worm tracks" after being reconditioned, it is recommended to dispose of it. Furthermore, any cored wire on plastic spools cannot go into an oven and are therefore not suitable for reconditioning and should be discarded if they exhibit any moisture related issues.

.
- Home
- News
- Contact us
- Stainless Steel
- Carbon Steel
- Nickel Alloy
- Low Alloy
- Aluminum
- Cobalt-Hardfacing
- Executive Line Card
- Find a Distributor
- Become a Distributor
©2024 Executive Filler Metals. All Rights Reserved.