Porosity is a weld defect characterized by the presence of cavities in the weld metal caused by trapped gas inside the weld pool as it solidifies. These cavities are known as spherical porosity but if they are elongated, the defect might be called wormholes or piping. It is not as detrimental to structural integrity as cracks, undercut, overlap or lack of fusion, however it is unsightly and when painted it becomes an eye sore. It does not propagate like a crack due to the lack of sharp edges, but it is unsightly, and decreases the effective area of a weld and therefore should be avoided.
Welding Porosity 8-24.pdf
Download
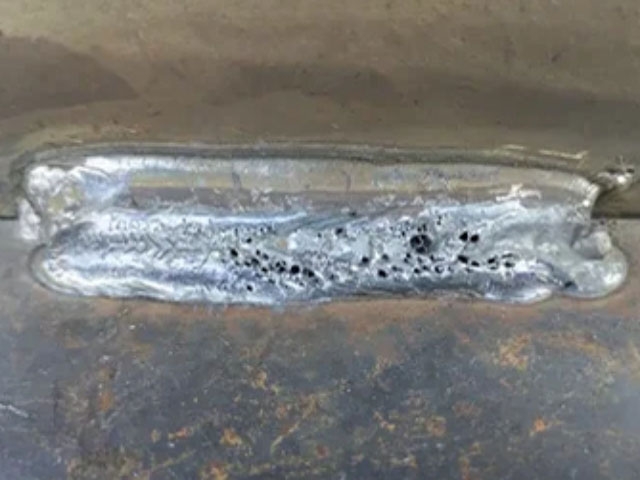
Porosity can be hard to troubleshoot since there are so many possible causes. However, many cases can be solved by doing one or a combination of the following troubleshooting steps:
1. Clean the surface to be welded
Contaminants such as moisture, grease, oil, cutting fluids, rust, paint and other sources of hydrocarbons will significantly increase the susceptibility to porosity as they release large volumes of gas when exposed to an arc. Materials with a surface coating, such as galvanized steel will present a problem. It is recommended that you grind off the zinc coating before welding. However, in some cases you are not allowed to do so. In this case choose a process that is more forgiving for this application, such as SMAW (Shielding Metal Arc Welding – Stick Electrodes) or FCAW (Flux Cored Arc Welding – Flux Cored).
2. Check your gas flow rate and equipment
If using a process that involves shielding gas, make sure you are running the adequate flow for your application and that the cylinder is not out of gas, also check for restricted gas flow in nozzles typically due to a build up of spatter. Contaminated gas hoses or gun liners can also introduce unwanted elements to the weld pool. In general, any wire process will usually require about 30 – 50 CFH. There is more variance in GTAW due to the difference in cup sizes, but in general you want to be between 20-30 CFH for this process. High flow rates (above 60 CFH) for wire processes can cause porosity as high flow rates cause a turbulent flow of the shielding gas which may introduce the atmosphere into the weld. If you must increase your flow rate past 60 to avoid porosity you may have other problems such as a leak in your gun assembly (see step 3), or potentially a strong draft (from a fan or from an open bay door (see step 4).
3. Check for gas leaks or kinks in hoses
Make sure all connections are tight. Check for damaged or kinked hoses. A gas hose longer than 20 ft. long is more susceptible to kinking. A common, but hard to find leak, sometimes occurs by improperly seating the back end of the gun into the receiving bushing in the wire feeder. Make sure it is as far back as it will go. Also check the O-rings on the power pin (end of the gun that slides into the receiving bushing) for damage. Even a small imperfection on the O-ring can be enough to cause shielding gas leaks.
4. Avoid drafty conditions
A draft caused by an open bay door or a fan even as far as twenty feet away can blow enough shielding gas away to create porosity. There are clauses of AWS D1.1:D1.1M:2020 Structural Welding Code - Steel, that prohibit welding for the GMAW, GTAW, EGW and FCAW processes if the wind velocity in the vicinity of the weld exceeds 5 miles per hour [8 KM/H]. If you cannot stop the draft or need the fan due to the heat, position your body between the fan and the weld. This also provides the added benefit of blowing the welding fumes away from your breathing zone.
5. Inspect for the presence of moisture
Simple condensation from welding on heavy plate and lap joints can cause porosity, especially if the temperature is below 50°F (10°C). An easy fix is to preheat the metal to 200 – 225°F (93-107°C) to evaporate any moisture.
6. Keep an adequate contact-tip-to-work distance (CTTWD)
This is usually 3/8" to 1/2" for GMAW short-circuit transfer and 5/8” to 1” for GMAW spray. Excessive CTTWD will decrease gas coverage as the volume of shielding gas reaching the weld is diminished and the dilution of the shielding gas with the atmosphere severely affects the weld.
7. Review the joint design If the weld joint is open at the root, it can draw in air from the backside, leading to contamination of the weld. An exposed molten weld pool is especially prone to absorbing air. Additionally, when performing GMAW on the edge of an outside corner joint, the awkward position of the nozzle can create challenges. The nozzle may not adequately cover the joint, leading to turbulence that allows outside air to be drawn into the weld joint, potentially causing defects.
8. Watch your travel angle. Keep it at 10-20 degrees from perpendicular (70-80 degrees from horizontal) whether you are pushing or pulling (See Figure 2). Excessive push or pull angles will create problems such as porosity, lack of penetration and excessive spatter.
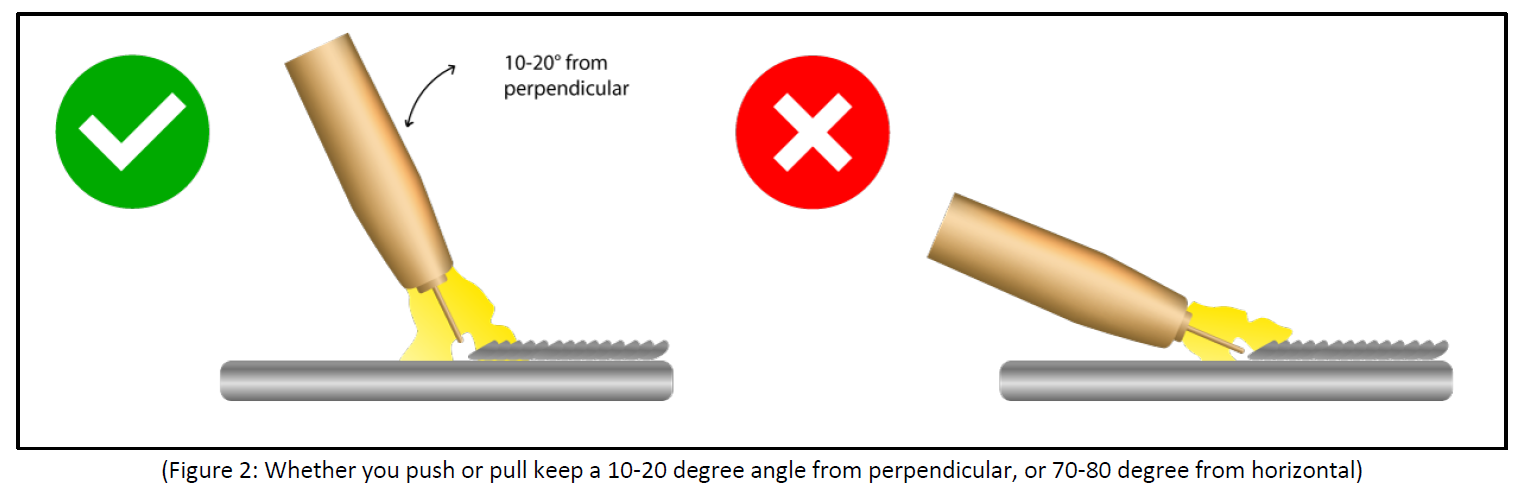
1. Use adequate shielding gas in a corner
When beginning a weld in a tight corner, the welder will need more than a little burst of gas that is released at the start of a weld. The operator should discharge extra shielding gas to purge out the corner pocket before the weld puddle starts.
2. Purge your gas line after a break
Lines can become pocketed with voids of gas after extended idle periods, such as after lunch or a break. The operator should run the gas for three seconds to ensure the line is full, cut off the wire, and then begin. At the beginning of each shift the welder should check for leaks by opening the cylinder, pressurize the system for 20 seconds, close the cylinder off, and then watch the regulator dial. If the dial begins to coast down in 1-2 minutes, there is a leak present, and the welder needs to find it.
1. Aluminium
If you are welding on aluminum porosity is much more of a problem than when welding carbon or stainless steel.
Everything that causes porosity on steel will have a greater effect on aluminum. Steel can tolerate higher levels of moisture, rust, paint, oils, etc. as carbon steel wires have deoxidizers that help reduce or eliminate porosity, whereas aluminum wires do not.
In conclusion, the causes of porosity are summarized above and none of them are instigated by the filler metal. If you are experiencing porosity and require additional troubleshooting assistance, reach out to your Executive Filler Metal supplier for more help tailored to your application and situation.
- Home
- News
- Contact us
- Stainless Steel
- Carbon Steel
- Nickel Alloy
- Low Alloy
- Aluminum
- Cobalt-Hardfacing
- Executive Line Card
- Find a Distributor
- Become a Distributor
©2024 Executive Filler Metals. All Rights Reserved.